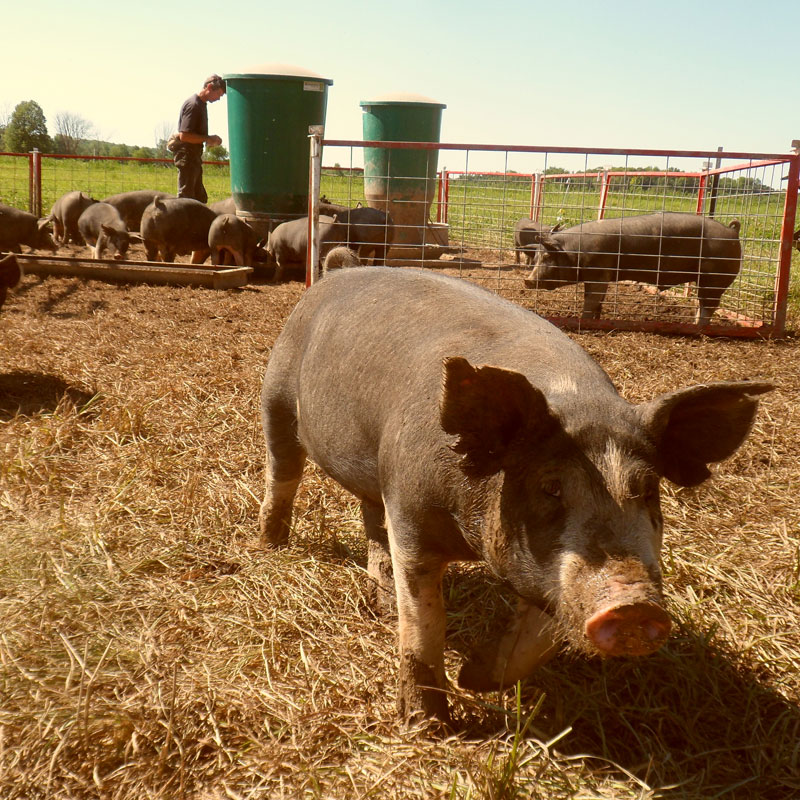
3 Tips for Raising Pigs Outside
September 30, 2019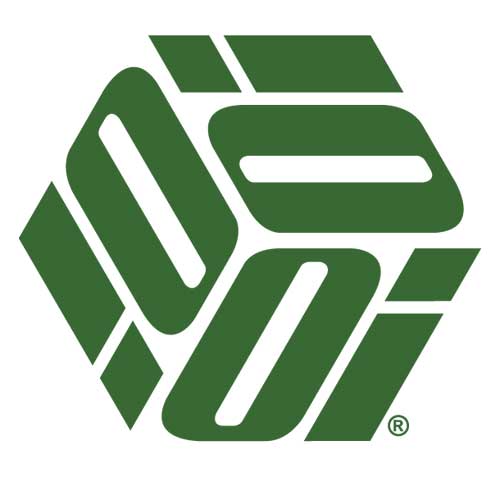
Special COVID-19 message from Osborne
May 29, 2020Molded thermoset plastic products offer numerous advantages over other plastic molding processes, including outstanding structural rigidity and strength and lower tooling costs. The molding process is crucial to reap the rewards of these advantages, but the properties of the materials used, like fiber-reinforced polymers or fiberglass-reinforced plastics (FRP), are what make these finished parts a success.
What is Fiber Reinforced Polymer?
Fiber reinforced polymer (FRP) is a composite material that consists of a polymer, like epoxy or a thermosetting polyester, and other reinforcing materials. The reinforcements are often fibers, which can be a variety of materials. Some examples include:
- Aramid – Results in heat-resistant synthetic fibers
- Carbon – Offers high strength, stiffness, chemical resistance and tolerance of high temperatures; also devoid of any magnetic properties
- Glass – Forms fiberglass that can be randomly arranged, flattened into a sheet, or woven into a fabric
FRP is known to be both high strength and lightweight. This material can even be as strong as some metals, which allows molds made from FRP to be applied to a large range of applications across industries.
The molding process typically associated with FRP is Resin Transfer Molding (RTM), a type of liquid molding. RTM is a closed-molding process that uses hydraulic pressure to inject liquid resin into a molding die lined with a reinforcement material (like fiberglass). The RTM process is appropriate for parts with complex structural additions, like embosses or ribs, yet offers high surface finish.
Advantages of Fiber Reinforced Polymer
There is a reason so many industries look to fiber-reinforced polymer for molding applications. Some of the many benefits of FRPs include:
- Excellent electrical and compression properties
- High-grade resistance to environmental components, chemicals and other corrosives
- Low-cost use of composite tooling in molding
- Structural integrity
- UV radiation stability
- Able to bond quickly with dissimilar materials
- Impressive thermal insulation
- Reduced weight when compared with metal components
Depending on the application, FRP can offer advanced material strength and more precise tolerances. FRPs are starting to be considered as an improvement on common infrastructure components like metal and concrete.
Common FRP Industry Applications
FRP applications have continued to grow as the material is becoming more well-known across industries. It has also started to be used in new ways, especially since there is ongoing development and advancement of FRP materials, such as high-performance resin systems and updated reinforcement styles.
Some of the industries for which FRP is most commonly used includes (but is not limited to):
- Automotive
- Aerospace
- Ballistics
- Biomedical
- Construction
- Civil Structures
- Marine
Contact Osborne Industries
The thermoset molding process known as Resin Transfer Molding (RTM) was developed and used by Osborne’s team dating back to the 1970s, well before it debuted as a standard practice. With our 45+ years of experience and a deep understanding of product development, you can trust Osborne to provide the highest quality manufacturing for your next project. Contact us or request a project quote to get started!